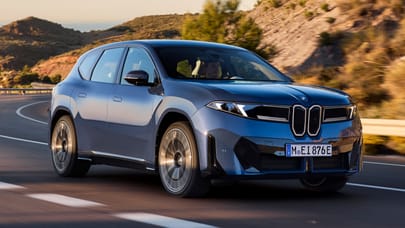
Eight things we learned visiting Hyundai’s new factory run by robot dogs
HMGICS isn’t your standard car plant. Prepare for salad farms, digital twins and robotaxis
We recently paid a visit to Hyundai’s new factory. You may be thinking “that’s not very exciting” and normally you’d be right – factory stories rarely are. But stick with us as this isn’t your usual, dull ‘bizness to bizness’ industry story. Because this isn’t your normal car factory.
It’s called HMGICS (or Hyundai Motor Group Innovation Center Singapore to give it its full – wordy – name) and it’s the industrious Korean brand's factory of the future: a vertical manufacturing testbed that runs like no other car plant.
How? Well, it’s FULL of robots. And has ditched the conventional conveyor belt workflow introduced by Henry Ford (and adopted in most car factories) in favour of a cell structure. This means multiple car models can be produced at the same time without constraints as different processes are performed independently in each individual cell. It also means Hyundai doesn’t need to just make normal cars. They can do scooters, drones, Purpose Built Vehicles (PBVs) and robotaxis all at the same time.
Now, that’s the dry bit done. Because the really exciting stuff is that this factory also houses as many robots as humans; some of which are dogs bossing humans around. There’s also a ‘digital twin’, robot salad farms, a rooftop test track, exoskeletal humans with chairs for legs, and autonomous robojanitors. It’s all very Black Mirror. And at this point we’re not sure to be excited or scared.
Here’s what we learned having spent the day sneaking around the place.
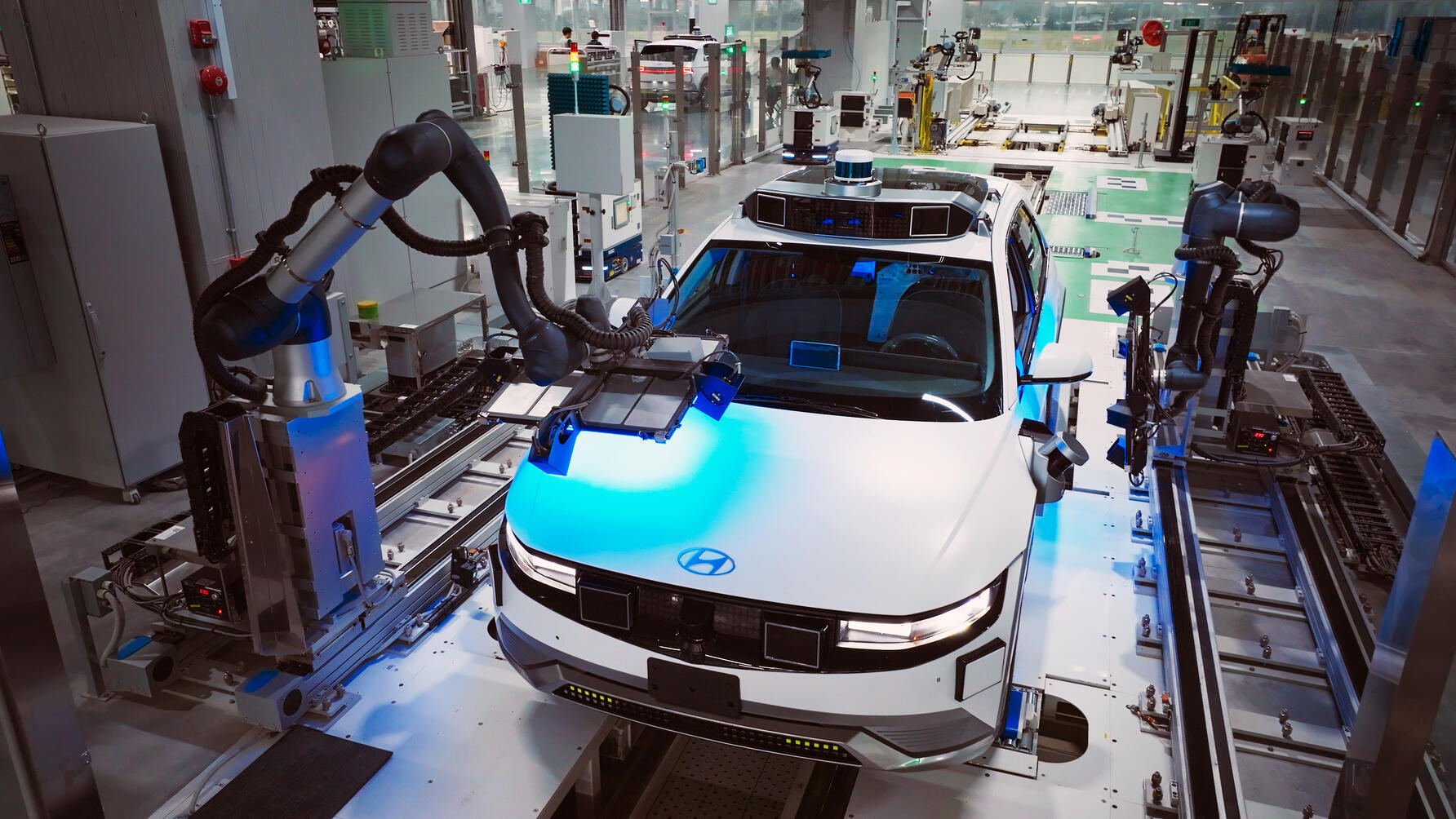
It’s turning manufacturing on its head
Hyundai is known for having a vibrant, pioneering and well-founded assiduous spirit. Remember, it’s the name behind the world’s largest car factory, the world’s largest shipbuilding facility and the world’s largest steel works. But HMGICS takes manufacturing to the next level.
Located in Singapore's western Jurong Innovation district, HMGICS is a snazzy and slickly lit 935,380-square-foot, seven-storey factory. Visually it riffs off breathy Scandi styling skewed with the minimalism and exaggerated emptiness of an Apple story. It may look 22nd Century, but it actually shares a lot of its thinking and DNA with another famous vertical factory: Fiat’s Lingotto. Which did it 100 years earlier…
Like Lingotto, raw materials are fed in at the ground floor and gradually work their way up the factory, becoming more car-like at every stage, before being spat out at the rooftop level to be pounded around the test track for final sign off. But where humans were a large part of that process in 1923 Italy, in 2023 Singapore those fleshy workers have been replaced with LiDAR and camera-clad bots that unload parts (no human lifting or forklifts here, so no bad backs or HR complaints either), transfer them around the factory, and park quicker and more efficiently than humans – saving space and time. Two key metrics in manufacturing.
The whole manufacturing process is overlooked by ‘Mission Control’. A glass box suspended above the factory where very brainy humans look at many, many screens and everything going on. Everyone has insanely tidy desks, big coffee cups and furrowed brows. It’s very Minority Report. But the humans are just feeding another machine: the Meta Factory. It’s the real factory’s digital twin that sees what’s going on so it can then simulate stuff for the future to maximise efficiency and fix problems before they’ve happened in reality. Eventually, it will theoretically run the factory itself.
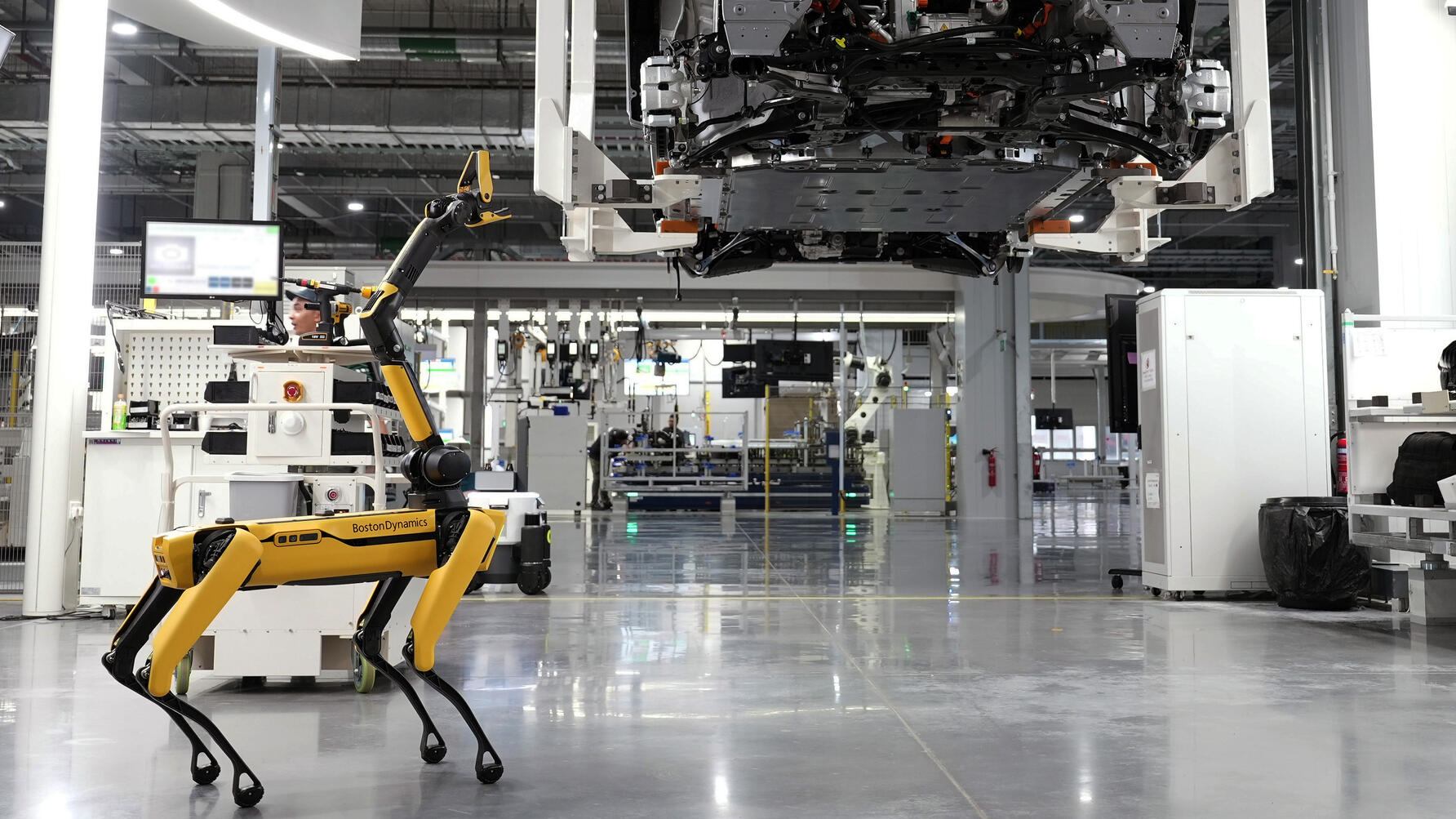
There are robot dog bosses
One of the strangest sights at the factory was Spot, a four-legged mechanical hound with a Viper-like neck and bite that’s in the running for the least cute dog in the world. Spot is the work of keen roboteers Boston Dynamics and has gone viral for classic doggy traits like being able to sit, fetch and digitally bark. And less doggy traits like opening doors. But Hyundai spent 12 months programming Spot to do specific quality-control tests in order to mark the human's car-making homework.
Top Gear
Newsletter
Thank you for subscribing to our newsletter. Look out for your regular round-up of news, reviews and offers in your inbox.
Get all the latest news, reviews and exclusives, direct to your inbox.
See, once one of the 27 fleshy human workers on the line has finished their tasks, Spot undocks from its high-voltage dog bed, scurries around the polished floor, extends its telescopic neck and begins scanning the Ioniq 5 for imperfections. Using very un-doglike camera technology, sensors and powerful AI, Spot takes photos of the assembly and uploads it to the cloud where it's analysed by vision AI to ensure that the process was done correctly. If it hasn't, Spot dobs the worker into the brainy people with the clear desks and big coffee cups in the glass box upstairs, then metaphorically barks at them to do it again. It’s rather odd to see this particular hierarchy in action. But it makes sure that your Ioniq 5 has fewer squeaks and rattles as Spot can catch errors that humans might not be able to see.
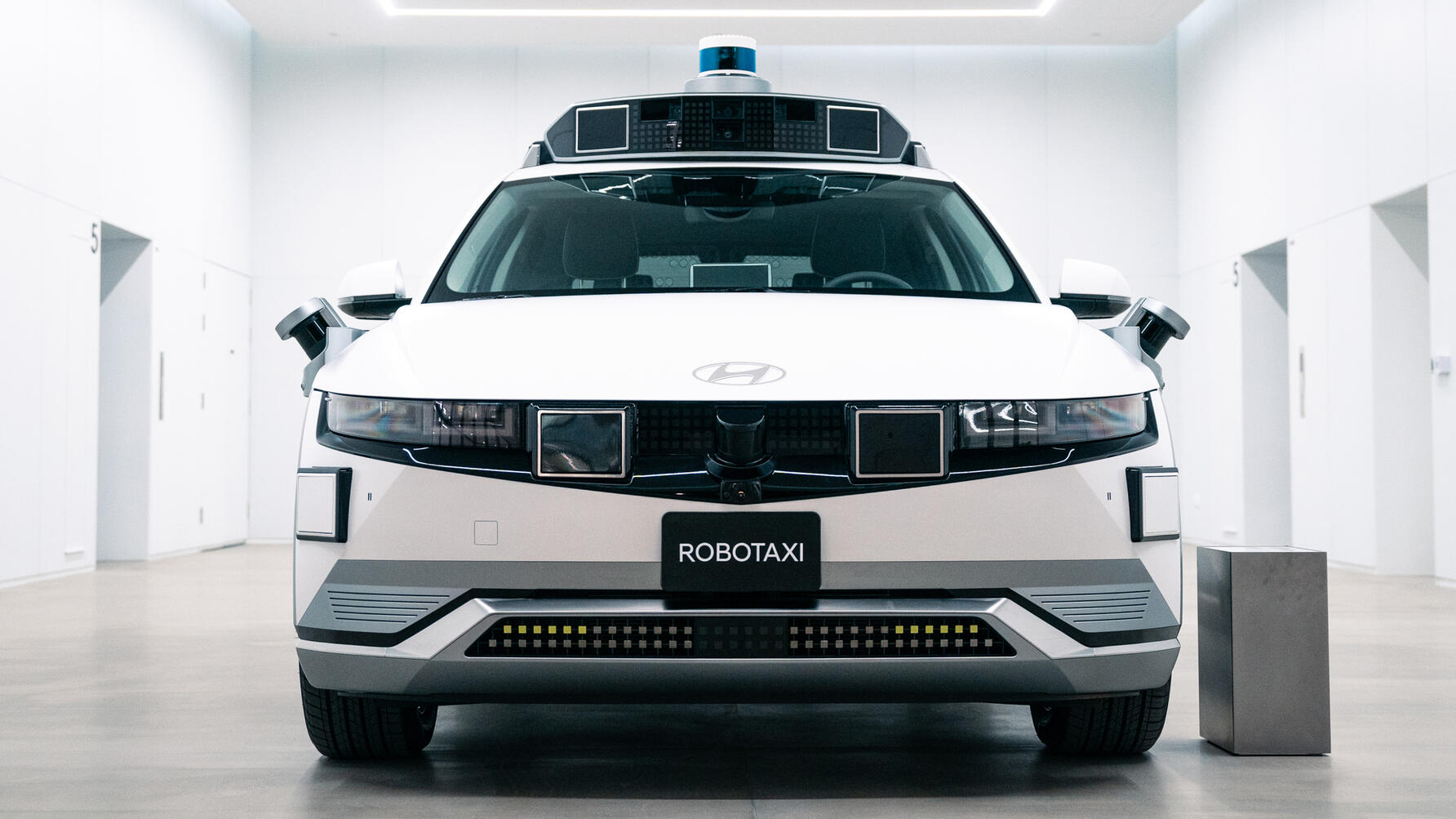
It's where they build robotaxis
Fed up with your Uber driver’s pneumatic throttle inputs and smelly chat? Well, that’ll be a thing of the past as this factory makes fully autonomous robotaxis. And they’re hitting the streets of the USA next year.
It’s part of a joint venture between Hyundai and automotive supplier Aptiv, whose company Motional has been modifying Ioniq 5s by fitting 30 additional sensors, LiDAR, radar and cameras and stuffing a load of computers and processing hardware in the boot so the car can drive themselves.
HMGICS is the only factory where Hyundai’s robotaxis will be produced and they’re currently being shipped to the USA as the first purpose-built and FMVSS-certified (Federal Motor Vehicle Safety Standard) autonomous vehicles. Currently, HMGICS can knock out 64 cars in a daily 8-hour shift. On a double shift, it could make 30,000 a year. Which sounds like a lot. But then you remember Hyundai’s Czech factory churns out more than 350,000 cars every year. But HMGICS isn’t about the mass market, it’s about a new process, personalisation and tailored service. Plus, for passenger cars (Ioniq 5 and soon to be 6) it’s only serving the tiny Singaporean market; a population of around 5.5 million (less than London) with less than a million private cars on the road.
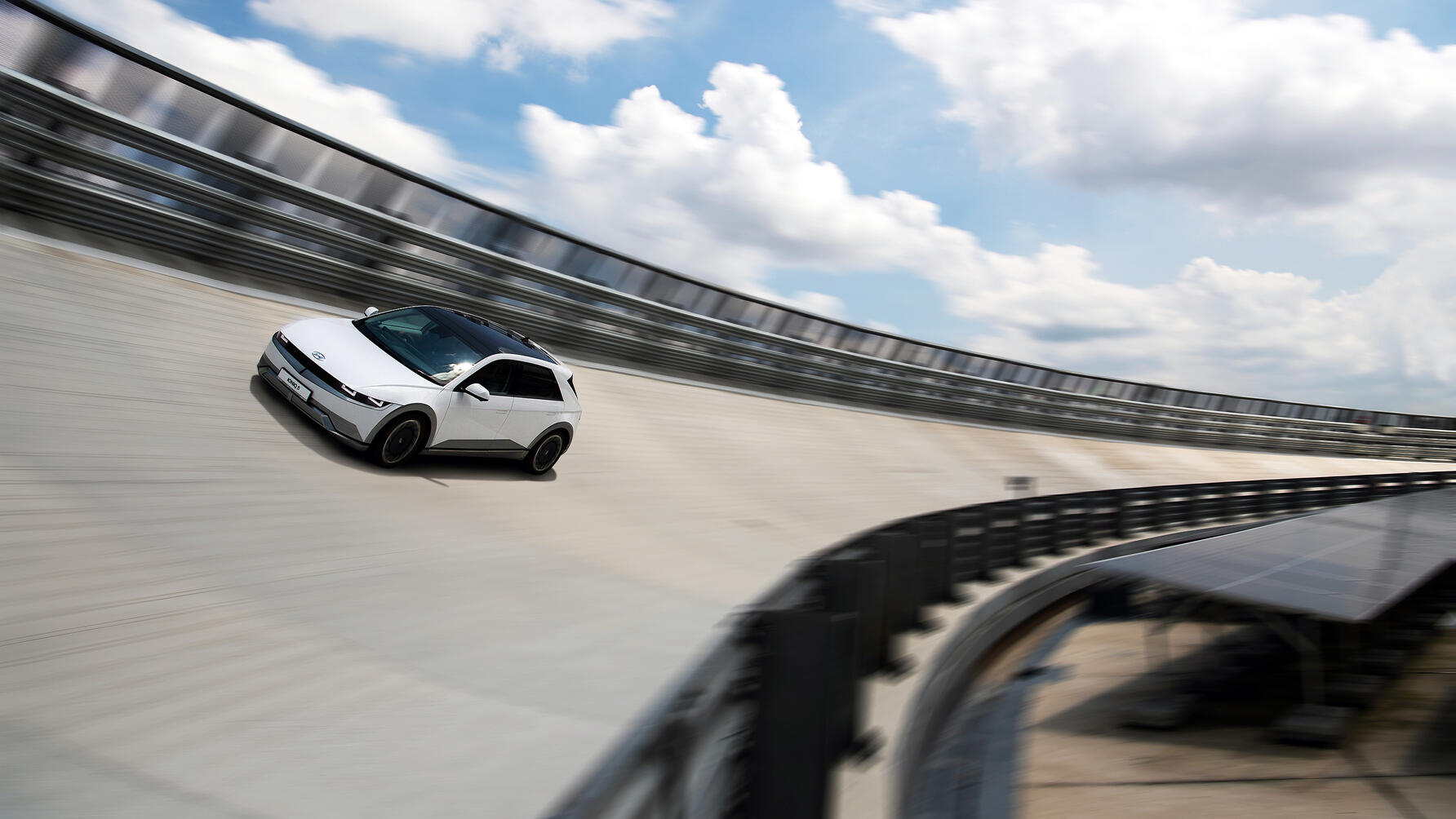
There’s a test track on the roof
Once cars have been built, a selection of test drivers (of the human variety) put them through their paces on the 'Sky Track'.
Unlike Nardo or other banked oval test tracks, the Sky Track is 28 metres off the ground and hangs four metres over the edge of the building like it’s Vegas’ Stratosphere rollercoaster. It’s also quite a bit smaller than Nardo, only being 620-metres long and with cars limited to a top speed of 50-ish mph. But that’s enough to make sure nothing is catastrophically wrong with the robo-assembled cars.
Each driver does three laps: one to test acceleration and braking, one to test wind noise and check off-centre steering and a third to nose it up the bank and test the hill assist.
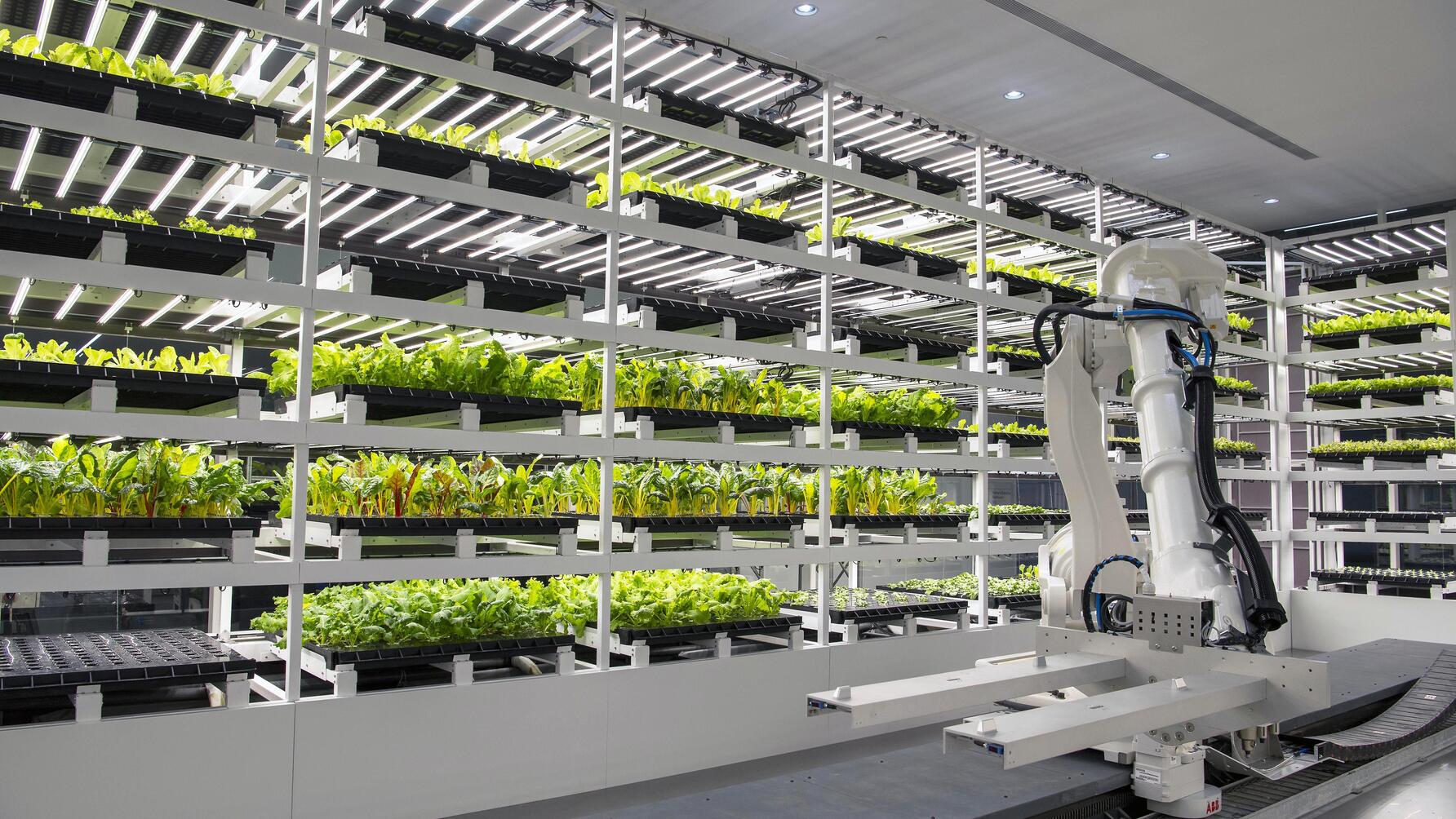
They make salad. Vertically.
In an attempt to show how forward-thinking it is, Hyundai has implanted (pun intended) two hydroponic farms on site. This is to prove that robotics can help in many ways, especially in a country like Singapore where 90 per cent of its food is imported and space is limited. As agriculture can’t be sprawling, you have to think vertically and reach for the stars.
HMGICS currently produces nine different greens (including romaine lettuce, chard, and mustard greens) thanks to five robot arms that process the crops from start to finish. They tend 568 "towers" that manage the crops' vitals: light, nutrients, humidity, and temperature. It takes about 50 days to go from seed to gob with "Mega Robot", a near 30-foot tall super arm overseeing everything, harvesting 250 crops a day. Which is good news if you’re a plant-based worker, as the canteen is rammed with leaves.
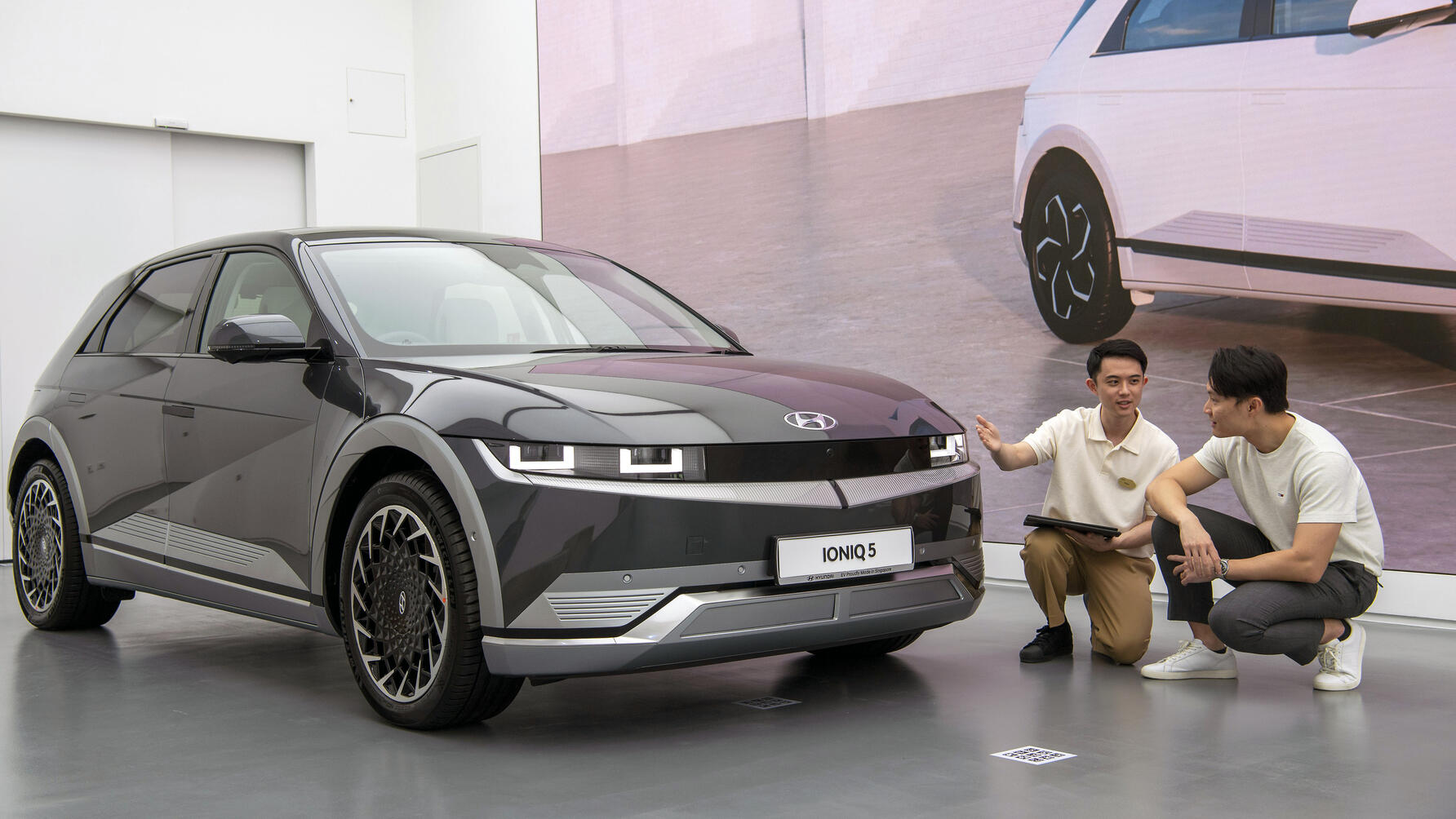
You can order a car like a drink in a vending machine
Singapore is the most expensive city in the world to buy a car. And the numbers will make you cry. See, before you even buy a car, to even be eligible to own one you must bid for a certificate that now costs £83k. Then you need to buy the thing... which is outrageously expensive. For reference, a Hyundai Ioniq 5 starts at £44k in the UK. In Singapore? It's £160k. Sheesh.
So buying a car is a big deal. Meaning service and personalisation are key. But also so is convenience. So in Singapore, customers can order a Hyundai from a smartphone app "from the comfort of their own home" or they configure their new Ioniq 5 via a glitzy Brand Experience area within the building.
After a quick VR tour of the factory, they can go all PTS on the colours, choose trim details, apply various wheels and even inject a little personality with a customisable centrepiece, such as insignias in the headrests or a 3D-printed dashboard. Once selected, the robots get to work and the manufacturing process begins. From start to finish is a few hours, so you have time to buy steering wheel-mounted tables from the gift shop (we’re not joking), have a salad and wait for it to come down from the test track upstairs and be revealed theatrically in a handover room before driving out the building with a substantially lighter wallet.
Human Workers wear exoskeletons
Where a normal car factory has 500 human workers, there are currently only 29 at HMGICS. They’re also highly skilled and doing more jobs than a traditional worker. But also blurring the lines as they have some bionic and digital intervention on their side to make working easier.
For example, while getting shown around the strip-lit line, I noticed a woman assembling door cards who had two chair legs strapped on. It was the best invention ever. Her legs literally turned into a chair. She would walk around like normal, then, instead of having to bend down and strain her back, she fell backwards and a passive lower-body exoskeleton caught her so she could half-sit on deployable legs.
Then there was a guy with a spring-loaded arm exoskeleton to reduce fatigue and strain when installing fasteners above his head but could also make anyone lift Atlas Stones like Magnús Ver Magnússon. Some workers even wore nifty smart glasses, which patched an augmented-reality display to view information and step-by-step instructions of their tasks so they can’t fail. It’s genius.
The Ioniq 5 is now a historical artefact
Considering HMGICS is the first manufacturing plant in Singapore for 40 years, it's quite a big deal. So as part of its ongoing collaboration with Singapore’s local government, when the factory opened last month, it donated the first Ioniq 5 manufactured to the National Museum of Singapore. Which should make school kids happy when they’re dragging their heels around it bored on a school trip. Or if you just happen to be on a layover on the way to Australia.
Trending this week
- Car Review
Nissan Kicks
- Car Review
Mercedes-Benz AMG GT