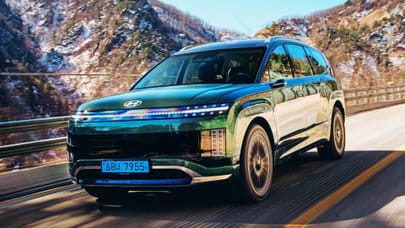
TopGear.com builds a 2013 F1 tyre!
I'd like to think that if Lewis Hamilton manages to pull off one of his daredevil, physics-defying overtakes this coming season and his car happens to be wearing, oh, let's say a yellow soft tyre, it's down to me. Actually, if any driver manages to pull off a world-class pass, I plan on taking the credit. I imagine the drama, the panache of the move, the glamour and the excitement. All me.
Truth be told, I had to keep this thought super-glued inside my head, because I was actually stuck in front of a hydraulic machine, in a factory sitting on a bleak, grim, uncompromising industrial estate about an hour's drive from Istanbul in Turkey. Far away from anything even remotely glamorous or exciting or dramatic. I was in a place called Izmit, at the heart of Pirelli's tyre manufacturing hub.
And I was building a proper, 2013-spec Formula One tyre.
Why? Simple really. Pirelli is facing the last year of its three-year contract to supply the tyres for Formula One, and by all accounts, they've done a ruddy good job of making F1 actually exciting. Like, really exciting. Paul Hembery, Pirelli's motorsport director - the chap you see on TV floating around the pits - told TopGear.com exactly what Pirelli was charged with when they entered the sport a couple of years ago. "We had clear input from FOM (Formula One Management) and Mr Ecclestone, that the racing had to be more exciting. We sat down with a technical group headed up by Ross Brawn, and the description we were given was to try and replicate the Canada race of 2010."
That race of course, was won by Lewis Hamilton (ahead of then new team-mate Jenson Button), and was filled with, as Paul notes, "a good deal of unpredictability and lots of overtaking." So when Pirelli stepped up in 2011, they introduced faster degrading rubber to bring ‘tyre strategy' into the game. And despite literally having a few months to work out the specific compounds to make the tyres, everyone was delighted with how fast the field suddenly got.
Well, nearly everybody. Schumacher was one notable critic of the new rubber, something Paul laughs off. "You're never going to please everybody," he says, smiling. "I spoke with Michael about it many times, but it depends on what your philosophy is of how Formula One should be. You could go for the maximum performance envelope - tyres, engines, aero all set to max - which the sport did, but that only ended up with processional racing.
"The fans left in their droves. We were asked to do something different," he adds.
And this year, Paul's promised even more drama, partly because Pirelli's philosophy is working, and partly because the cars aren't drastically different from last year. "That means we have to be slightly more aggressive," he says. And by aggressive, he means changing the structure of the tyre, and it's here where it all gets a bit complicated...
"We've made a change so that this year's tyres have more grip mid corner - what you would call ‘combined traction'. We've also added to the rigidity of the belt package, the area just underneath the footprint, and due to these changes we've added 700g to each rear tyre, and 200g to each front tyre."
It's a big change. There are six different compounds: intermediate (green), wet (blue), medium (white), hard (orange), soft (yellow) and super soft (red). The tyres might look like simple blobs of rubber glued to an alloy, but they're highly complex composites made from lots of different materials and subjected to incredibly high pressures even before they leave the factory.
Top Gear
Newsletter
Thank you for subscribing to our newsletter. Look out for your regular round-up of news, reviews and offers in your inbox.
Get all the latest news, reviews and exclusives, direct to your inbox.
And we're in the factory that will produce all the Formula One tyres for this season. In Izmit, the research and development chief Bahadir Ozer guides us around our flailing attempts at putting together something quite complicated. There's an oft-quoted Top Gear maxim that could apply here...
"The whole tyre building process starts from our, ahem, ‘secret area'" he says, with a wry smile, pointing to a closed-off section of the factory. What happens is the chemistry boffins in Milan send over the compounds to Turkey, where they're put together. But because this is a very secretive compound, nobody's allowed to look at it. Not even TopGear.com.
Once the compound is made it goes into the main factory, where part-automated machines put together the building blocks of the tyre. First, there's a rubber sheet that forms the tyre's inner liner - a sort of tyre-shaped drum - that gets put onto a spinning machine. And here's where TG.com comes in. We have to apply the ‘ply', a sort of rubber sandwich (two layers of rubber with reinforcing material in-between), a sidewall (the bit on your normal tyre with all the sizes and lettering on), and a bead, which is a ring of very strong metal that forms a seal with the rim. It's quite difficult. Some Pirelli workers frown. I may have ruined a few tyres in my attempts.
Next comes the actual belt package Paul mentioned before. It's a combination of rubber sheets with steel cords inside, and once this is all assembled, the semi-finished tyre gets sent over to the ‘curing' department. Sounds disconcerting, and it is. Here, the tyre is slotted inside a specially-built metal mould, which gets inserted into a very large, very hot and very scary machine that pressurises and heats the tyre up to 200 degrees centigrade. The reason for this pressure and heat is to bond all the various materials together into one happy tyre. It's also here where the FIA barcode - each tyre has its own barcode - gets ‘hardcoded' into the tyre. And every tyre is scanned to track exactly where it is, who made it, when it was made, etc. It's all a bit 1984.
Once it pops out of the oven, it gets passed over for a visual inspection, then an x-ray check to inspect the spread of the materials inside, and finally a check for any imbalances. Once this is done, it's transported to the other side of the factory, and stored in a warehouse that's temperature controlled and has a capacity to house 22,000 tyres - including other motorsport disciplines such as rallying.
And if you want more stats, how about these: in an average year, this factory - which began life in 1960 and made its first tyre in 1962 - pumps out seven million tyres each year, 45,000 of which will go to Formula One. They make 10,000 prototypes ahead of the season for Pirelli to test around the world too (around 7,000km worth of hard driving). Pirelli reckon the finished tyres will be 0.5 seconds a lap quicker than last year, and once up to working temperature, these F1 tyres will hit 110 degrees centigrade.
And that's kind of the point - to get them up to temperature quickly - and assist in overtakes. "Warm up times will be reduced," Paul tells us. "We're hoping to create a challenge of thermal degradation which we saw quite a lot of in 2011. They help overtaking then, because what you get are differences in chassis setups and driver styles, and different points in the race where somebody might have changed their tyres, so that basically changes the overall speed.
"Cars can lap at different pace, and the idea is if you have different pace, you have an opportunity to overtake. We're changing the absolute relative lap times from one car to another," he says, as though he were reading the name of a biscuit pack. Clever chap, this Paul is.
And it's here, in this grim, monotone factory full of rubber and chemicals and Terminator-esque machines where Formula One gets its glamour and excitement. Because Pirelli can make or break this year's championship. As can TopGear.com. On cue, our F1 tyre pops out of the oven. It looks round. It looks rubbery. It looks yellow. Maybe, just maybe, we did something right? Some Pirelli men force fake smiles. There is some strained laughter and nervous glances. F1 driver chaps, a little note for the coming season: if you happen to come across a yellow soft tyre that looks a little...wobbly, please accept TopGear.com's humblest apologies. Ahem.