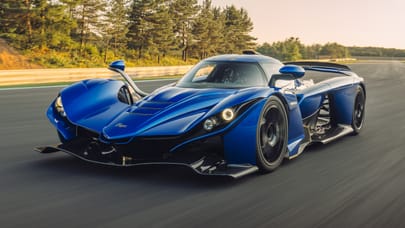
Eight things we learned about Red Bull’s factory
Taking a walk through Red Bull Racing's technical centre is like filling your mind's internal fuel tank with nitrous-tinged super unleaded.
This is the place, after all, that has conceived, designed, engineered and built four Formula One cars that have won consecutive world championships. From 2010 to 2013, Sebastian Vettel won the drivers' title, while RBR took the constructors' crown. It's an astonishing achievement.
Ahead of this year's Belgian Grand Prix, we had a poke around the place that Sebastian Vettel and Daniel Ricciardo call ‘the office', a factory floor built of excellence, ingenuity and the contents of Adrian Newey's GIANT BRAIN.
And here are eight things we learned about Red Bull Racing's Milton Keynes base.
They have a Room Of Death for parts testing
We weren't allowed to go into this part of the factory. And we were quite pleased about that, because within lies a veritable torture chamber for the parts on Red Bull's F1 car.
It exists so that every single part that appears on the final weekend racer can withstand the pressures, twists and forces exerted upon it by an ambitious racing driver and an unrelenting circuit/other drivers, just to see how long they last before they pop.
18 engineers and technicians work a variety of machines to make sure everything is strong and up to the task.
They have a machine shop that manufactures its own parts
24 hours a day, seven days a week, the machine shop churns out part after part; in fact, more than 1600 parts are ‘processed' in just one week.
They have 19 ‘five-axis' milling machines, three wire and spark eroding machines, and six manual machines, each worth anything between £250,000 and [cue Dr Evil close up] £1,000,000.
These machines can build any metal component on the car, using a combination of 60 different metallic materials (steel, titanium, aluminium, magnesium - you name it); anything from the gearbox to the chassis. Maybe not your Stig metal keychain, though.
They can design and build a part in just one day
It's that simple. In some extreme instances, Red Bull's Milton Keynes factory can design, build and ship a part in just one day. Sometimes, it's specially wrapped and carried on as hand luggage on commercial flights. In amongst the cheap booze and fags, naturally.
They build all their own carbon fibre parts
A crack team of Men In White Coats operate in the composites department building the carbon fibre bits on Seb and Danny's car. Over the course of one season in Formula One, the factory produces 10,000 parts which are delivered to the race team.
Once built, it then goes to the next stage...
They cook carbon fibre parts in four Giant Scary Ovens
This is used for literally baking the carbon fibre parts built by aforementioned Men In White Coats. The ‘autoclaves' sometimes run 24 hours a day, operate at 100PSI and cook at 180 degrees.
Also, the door of the Really Massively Giant Oven has more than 600 tonnes of internal pressure trying to force it open when in use. Probably best to cook your pizza in something else, unless you want to turn it into a diamond.
They practice pit stops on the factory floor every day
Last year at the start of the 2013 F1 season, Red Bull Racing set a new pit stop record of 2.05s. Later that year at the Austin Grand Prix, they blitzed this with an astonishing 1.923 stop for Mark Webber, making it the fastest ever Formula One pit stop... in the world.
How is this possible? They've got a dedicated section on the workshop floor that's solely for doing these stops. RB have even changed the quality of the floor over this section alone to match the tarmac on the circuit - it's grittier than the shiny factory floor.
They have a co-ordinate measuring machine that looks like a LASER
It's a machine that essentially probes the parts built and then scans them into 3D to make sure everything tallies up to Newey's perfecting design.
OK, so it's not actually a frickin' laser, but it sure looks like one. Cue Goldfinger quotes...
They have an ops room that has a better internet connection than most countries
A team of engineers operate in real race time in this little room, providing trackside support to whichever circuit RB is at. More than 100GB of data is transferred between the factory and track, covering everything from car telemetry, GPS, FIA control system, radio messages and video.
Thankfully, their internet connection appears to be significantly more advanced than Top Gear's.
Top Gear
Newsletter
Thank you for subscribing to our newsletter. Look out for your regular round-up of news, reviews and offers in your inbox.
Get all the latest news, reviews and exclusives, direct to your inbox.
Trending this week
- Electric
Top Gear's top 20 electric cars