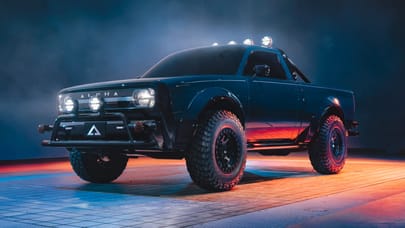
Nissan Sunderland: 13 stats about the UK's biggest car factory
Japanese carmaker's giant UK plant takes big data by the wiring harness and shakes out some pub quiz trivia treats
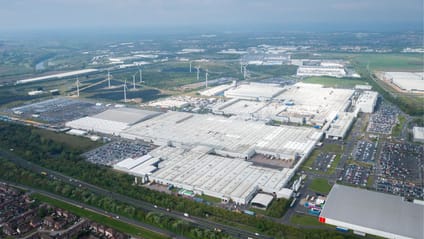
Only 30 per cent of applicants get recruited
The hiring process involves completing 10 rotations of five tasks in less than 16 minutes, and TopGear.com was astonished to discover not one of these tasks involved a tea round. Only 30 per cent of applicants cut the mustard, and the current record stands at nine minutes. Bravo.
Advertisement - Page continues belowTen wind turbines account for almost half the renewable energy Nissan produces
Ten turbines generate seven megawatts of renewable energy; that contributes to a total of 17MW the plant makes on-site. Originally built on RAF Usworth land, the MoD initially restricted the number of turbines Nissan could deploy. Those limits have now been relaxed. Apparently, fitting longer blades to the existing wind turbines (24ft to 25ft) will improve energy generation by up to 16 per cent.
Two solar farms with 78,000 panels generate 10MW of green energy
There are two solar farms on site, and each one deploys 39,000 panels to produce five megawatts. So 10MW in total from solar power, which added to the seven MW from the turbines adds up to 17MW. Nissan’s ambition is to use 100 per cent renewable energy, but at present it can only achieve 20 per cent on even the sunniest/windiest day. Yeah, welcome to Britain.
Advertisement - Page continues belowNissan needs 32MW to produce 100,000 cars
Though, while it's churning out 17MW at the moment, 32MW will give Nissan enough power to produce 100,000 cars with carbon-free energy. With the capacity to spit out 600,000 cars per year, by our maths, that's, erm, 'lots' shy of making the whole plant renewable. Good luck, folks.
The Battery Assembly unit can build 250,000 packs
Nissan’s smallest area of the facility measures 5,400 sq metres, and it's the only department that runs three shifts consistently because it needs to keep up. A car rolls off the line every two minutes, but it takes 4.5 minutes to complete the battery pack build. Techies use a fancy video-gamified programme (OSG) to build out the 1.8kWh packs for e-Power and hybrid models, so tell your parents you can put all that gaming practice to good use after all.
It takes 14 hours to build a car
The 13-tonne steel or aluminium rolls arrive at the plant and within six hours, they’re being used to stamp the body panels fabricated on-site. After 14 hours, a complete car leaves the line ready to be put on a transporter to head to Tyne Dock, where they're shipped to the rest of the world.
Two giant five-tonne+ presses create the body panels
The weight of the presses stamping out Qashqai and Juke panels is mind-boggling - 5.4-tonne and 5.2-tonne presses on each of the lines stamp the dies together. It’s the equivalent of 54 cars, or 26 EVs (respectively), simultaneously landing on a wafer-thin piece of material. Nissan tells us it’s saved 60 per cent in weight versus the current Qashqai by using aluminium in the new hybrid version, to both boost fuel economy and green smarts.
Advertisement - Page continues belowA 400bhp shredder spins the waste metal at 150mph to prep it for reuse
'The Cyclone' sounds like a villain from a comic, but this one is a hero. Sucking the waste steel and aluminium from the press shop into a 400bhp shredder, it uses speeds of 150mph to syphon the tiny pieces into 15 trucks per day. The recycled metal saves 90 per cent energy versus using newly processed stuff. What a twist.
There's 11,120 square metres of panel storage
Since it fabricates its panels on-site, Nissan needs a big space to store them all. And it is big. It's twice the size of the Battery Assembly area, used simply as a massive cupboard. The entire plant - as we mentioned in our beginner's guide - is a whopping 362,000 square metres in size. Woah.
Advertisement - Page continues belowDancing arms do 1,500 spot welds per car safely
As of 2023, Nissan's welding has been 100 per cent done by robots, which, it says, means more precision and better safety. Each car gets 1,500 spot welds from dancing robotic arms that we definitely haven't just added to our nightmare 'machines-taking-over-and-enslaving-us-all' scenarios.
The paint shop is kept at a constant 23 degrees
The paint shop is kept at a consistent 23 degrees celsius so those robot arms don’t lose their cool. Go two-tone and you can guarantee you gave someone in the department a job to do that day, since all masking is done manually by a human.
Each metal shell is base sprayed and primed, then colour-sprayed. Then they hit a 90 degree oven for eight minutes to put a skin on the colour coat before two lots of Shellac-style chip-resistant clear coat are applied. Then comes a top coat which cooks at 140 degrees to cure. Remember this fine, solid work next time you spot that errant supermarket trolley in the car park.
Almost one million components arrive every day
One million parts come to the plant from 500 global suppliers. In each department they’re sorted into kits – like Lego - so each technician has exactly the number of parts needed for each unit.
14 minor defects are found in every 100 cars at final inspection
Over 975 checks are done over the course of the build of each car to keep the final inspection defects to a minimum. It means the 14-in-every-100 cars is a pretty impressive low.
Trending this week
- Car Review
Nissan Kicks
- Car Review
Mercedes-Benz AMG GT