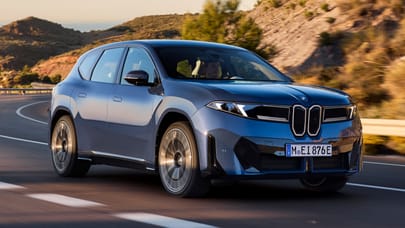
Behind the scenes at a live Mercedes-Benz electric car crash test
Merc’s experts reveal what goes into crash safety… by smashing two cars together
“The car is not important!”
As a tagline for a [checks notes] car company, it’s right up there with ‘wouldn’t you really rather have a Buick?’ (answer: would really rather not, thanks). Though one really rather suspects the author of this slogan – Paul Dick, Mercedes-Benz’s vehicle safety boss – doesn’t care about marketing one-liners. He’s a serious man with a serious mission. And without hesitation, he’s already off.
“We have a roof test which is our own internal requirement – it’s not a regulation,” he tells TG. “It’s a special test. Half a metre from the ground we drop the car onto its roof. We see from our field research that a lot of accidents happen with ‘overlap’. Where does it come from?”
He fixes a stern expression and gestures playing with a mobile phone. “More and more, like this,” he says. “Don’t do this. You lose focus on the street for just a second and then a child appears, or another car, or a bicycle, or a sharp curve.” And then, well, y’know.
Or maybe you don’t. There are 1.3 million road traffic fatalities every year, the equivalent of 12 large airplanes crashes a day. “We are not in the mood to accept this,” Dick says. Which is why he spends his days sending massive Merc tanks into one another at speed.
He started his days at Mercedes 22 years ago, putting his education in materials forming to use shaping aluminium, high strength steel, hot stamping and hydroforming. “I started my career in the prototype shop,” he says, “but it’s interesting because throughout my career I was always connected to the safety guys. In the prototype shop we have to get the ‘body-in-white’ very stiff and rigid.”
He then spent five years working on corrosion protection, then to developing the body-in-white, and has spent the past two and a half years as the director of vehicle safety. And as director, he outlines the four safety ‘phases’.
Phase one is driver assistance to avoid an accident – you’ll be familiar with the myriad electronic guardians on board a modern car. Phase two is bracing for a possible impact (Merc’s ‘pre-safe’ tech that does things like tension the seatbelts and so on) while phase three is protecting the occupants if an accident is unavoidable. And that’s where “intelligent material technologies” come into play.
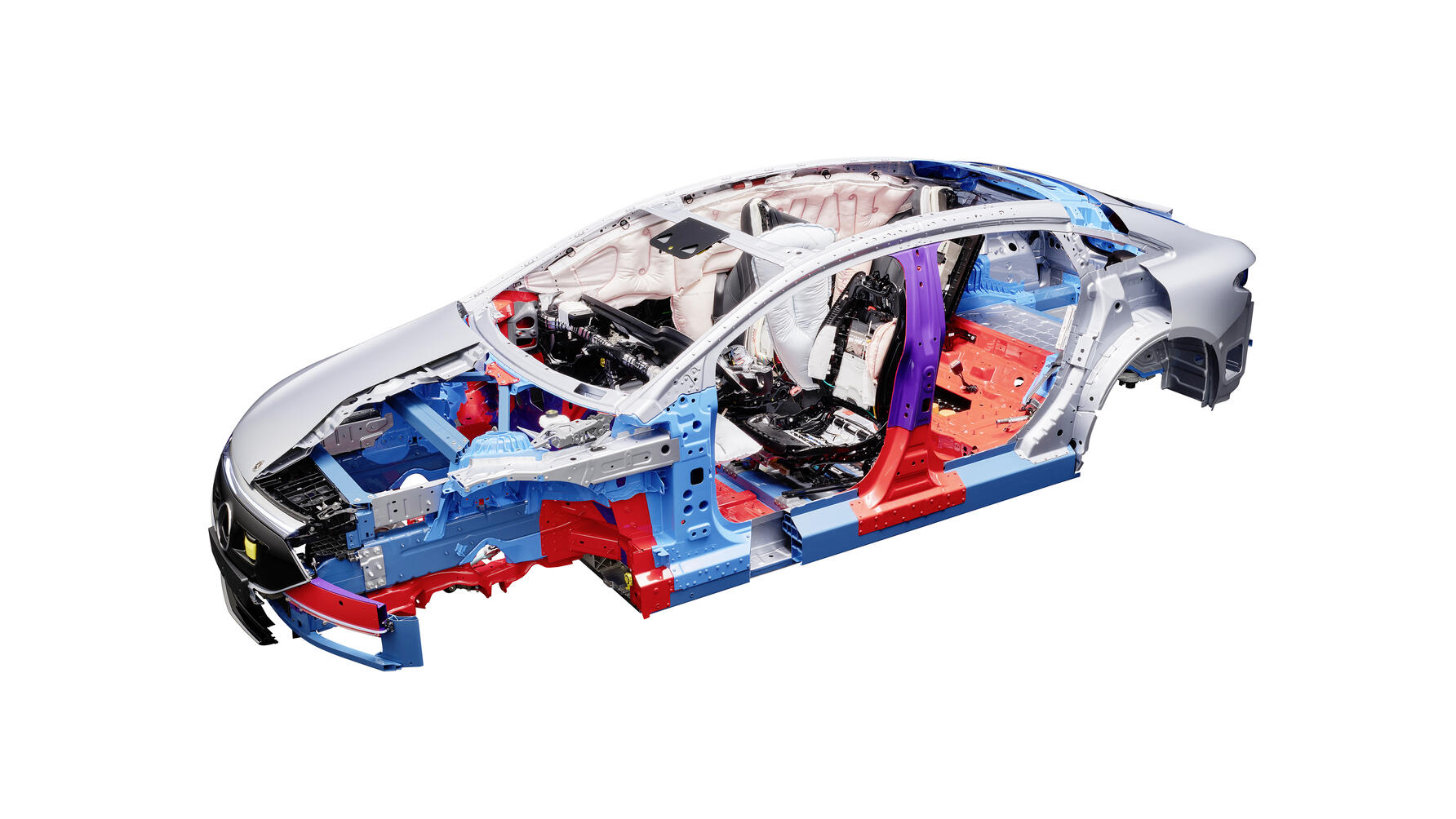
Look at this cutaway of a Mercedes EQS saloon, and you’ll spot the range of materials in play here in various places. The light blue sections are all cast aluminium, while red is high-strength steel. The darker blue points are made from extruded aluminium parts, while that purple B-pillar is hot formed ultra-high-strength steel. Naturally there’s regular steel (dark grey) and aluminium sheet metal (light grey) dotted about too.
“We are working on a lot of used, recycled material to have a closed loop,” Dick says, “especially with aluminium. We already use recycled steel in our cars.” They’re currently working on making castings even more lightweight.
Buried within this rigid, multi-material body lies what passive safety engineer Julia Hinners calls the ‘safety brain’: a small yellow box that takes data from the car’s myriad sensors, and decides exactly what to do in the event of a crash – like, for example, what airbags to deploy (from front, to side, to belt) and at what stage, to then shutting down the high voltage circuit for EVs.
It all points to the reason for Dick’s earlier proclamation about why the car doesn’t matter.
“We are working on saving people’s lives,” he says.
A lot of crashes are car to car, Dick explains – overtaking, crashing into each other, this 'overlap' mentioned up top. “So if you have a big car and a small car, we have to look at how they interact with each other. You need the space [for the car to deform safely] and ensure the room inside the cabin is safe.
Top Gear
Newsletter
Thank you for subscribing to our newsletter. Look out for your regular round-up of news, reviews and offers in your inbox.
Get all the latest news, reviews and exclusives, direct to your inbox.
“Therefore we need the right material in the right place. Like in an EQS or an S-Class, you can put in ‘profiles’. Aluminium profiles absorb a lot of energy, a lot more than steel, but a smaller car like an EQA needs high strength steel,” he says.
Mercedes conducts accident research within Stuttgart itself. They’re in contact with the county police, who alert the team to an ‘unusual’ accident – something the team haven’t yet experienced or encountered. “We want to learn about that collision scenario, about what happened, the scenario right before, how the drivers behaved. It can be a little tricky, and we of course have to get consent," says Hinners.
“But when we do we gather a lot of information, document the deformations and talk to the occupants about their injuries,” she adds.
Speaking of deformations, Mercedes is keen to stress that the level of safety isn’t dependent on the drivetrain, though electric cars naturally require different attention. Without the massive combustion engine lump up front for example ass a block, says Hinners, engineers can develop front profile structures “exactly as we want”. The floor-mounted battery is surrounded by extruded aluminium with lots of space, “to allow deformation outside the cells”. This keeps the battery safe in the event of an accident.
Ah yes, the accident. The live crash test – the first public test Mercedes did involving a pair of electric cars – was, if you’ll excuse the unintended pun, shocking. Conducted in a large facility that feels like it could double for a Half:Life set, replete with all manner of photography, video and lighting equipment, a gazillion sensors and an EQS SUV and EQA, it showcased the results of ‘the most frequent type of accident’.
Mercedes’s test far exceeds what Euro NCAP requires: this one was faster and involved two live cars much heavier than needed. And nothing can prepare you for how horrific it is, even in such controlled circumstances and filled only with crash test dummies.
Indeed, those dummies feature a tonne of sensors measuring all manner of physical loads. Hanna Paul, Merc’s dummy-technology engineer, explains how the data these sensors generate in an accident are reported. “Depending on the body region, they’re then linked to the probability of injuries. We generate a lot of data. Imagine you’ve got 150 sensors in each dummy, and you have up to four dummies in each car, and then you have additional measurements taken inside the car. There’s a tremendous amount of data generated for each crash.”
Consider Mercedes conducts three crash tests per day, and up to 900 per year, and you get some idea of just how much data it’s logged over the years. While dummy technology started in the Sixties, female and child dummies were only introduced in the early Noughties, improving the quality of the data to account for different biomechanics and body sizes. Paul stresses Merc doesn’t build the dummies, but are actively monitoring the development, and there’ll be greater advances in this technology in the future.
A future in which Mercedes wants to wipe out road fatalities altogether. Much like Volvo, the company is working on a lofty target. “We don’t just want zero traffic fatalities by 2050 and a halving in the number of traffic fatalities and serious injuries by 2030 compared to 2020,” said Merc’s technology boss Markus Schäfer. “Our goal by 2050 is zero accidents involving a Mercedes-Benz vehicle.”
Turns out, the car is quite important.
Trending this week
- Car Review
Nissan Kicks
- Car Review
Mercedes-Benz AMG GT