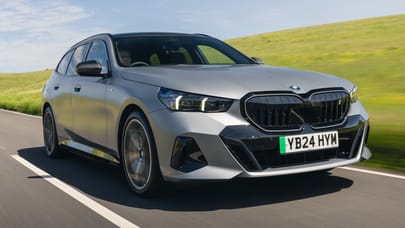
SPEC HIGHLIGHTS
- SPEC
DBX
- ENGINE
3982cc
- BHP
550bhp
- 0-62
4.5s
How to build an Aston Martin DBX
All too often we drive our cars around, completely oblivious to the scale of complexity in their design and engineering or the skill and care that has gone into their construction. A day spent at Aston’s St Athan facility brings that skill and complexity into sharp focus.
The build of the DBX features four key stages: Body in White (20 stations), Paint Shop (40 stations), Trim and Final (50 stations), and Off Tracks (18 stations). The car spends roughly three days in each of the four areas, each station/process taking an average of 27 minutes. So, it’s going to be a long shift. That’s right: we’re here to build TopGear’s very own Aston Martin DBX.
We start in the paint area where racks of painted DBX shells hang three tall and six wide. The precision of the robot painting process is truly mesmerising. But much as I could happily stare at it all day, we have a car to ‘build’.
We move from Paint by a gantry over prep bays (where the Aston team fastidiously polishes, buffs and finesses any imperfections) and arrive at the assembly line. I’m let loose on the big expensive digital torque wrench that connects the engine and transmission to the subframe.
This involves manoeuvring the 4.0-litre V8 AMG engine and transmission precisely into position and then letting the torque wrench do the work. My first attempt at using the hoist is best described as amateurish, but the second ends with the satisfactory beep as each bolt is torqued up and registered in the system.
From Powertrain we shift to the interior department where I am shown how to assemble and dress the front seats with their Bridge of Weir hide, and then spend some time removing any imperfections using a heat gun.
I provide a few minutes entertainment as I flail around trying to fit the leather cover over the metal and foam armature. Thankfully I’m better at the imperfection removal with the heat gun. Chuffed at not having got distracted and set fire to my new seat, it’s time to visit ‘our’ Aston and see how it’s progressing.
We join it well through its build at an essential stage… and one perfectly designed for the skill level of the journalist. Bolting the wheels on involves lifting the wheels into place using a gadget that makes light work of the lifting part and bolting them on with a five lug wheelgun that measures and registers the torque of each nut. Perfect for my skill set, but sadly the line team was so keen to go to lunch that the wheels are already bolted on. The production line waits for no-one.
In all, a DBX features roughly 14,500 parts, and the afternoon sees me ‘help’ with the insertion of the seats and placement of the steering wheel but mostly marvel at the skill of the team who ducks, dives and dodges in and out of the DBX with seemingly impossibly large components, deftly fit them then head on to the next stage.
Sadly, building the DBX is where my part in its life with TG ends as I head off to pastures new. Whoever is lucky enough to get to run it will be driving a piece of fabulous engineering - but I’d definitely check the wheelnuts are tight and the steering wheel alignment is true...
Featured
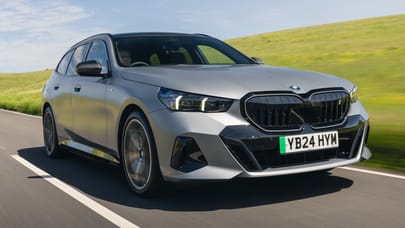
Trending this week
- Car Review
Nissan Kicks
- Car Review
Mercedes-Benz AMG GT