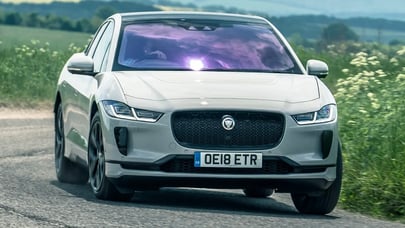
Every Formula One car wears something built by a British bloke in a shed. A statement which, when you consider the torrents of cash that flow through F1, seems a tad fantastical. But there's a very real, very skilled army of motorsport experts hidden in our drizzly industrial estates, without which the sport simply wouldn't exist in the same form.
And seeing as the 2012 Formula One season wraps up this weekend, we thought we'd round them up and celebrate their unsung contribution to the world's most glamorous race series.
Click on and join us for a cup of instant coffee and a Digestive as we visit every single one of them...Advertisement - Page continues belowZIRCOTEC
Sat on land consecrated by the original MG factory, Zircotec supplies some form of its nuclear-grade heat-protective coating technology to every F1 team on the grid.
And good lord, this stuff's clever. The coating protects vulnerable composite parts from getting damaged by heat - so stuff like carbonfibre brake guards, engine airboxes and floors -by applying a 0.3mm layer of ceramic.
But this isn't Ming Dynasty spec - it's a special concoction that only sticks to stuff when it's applied with a 14,000°c flame at twice the speed of sound. The method uses so much power that Zircotec has to have its own substation (its electricity bills are £5000 every month).Once it's on there, it can reduce surface temperatures by up to 50°c, allowing closer packaging of equipment and protection for hitherto unusable lightweight materials - the resin that holds carbonfibre together, for example, would melt without the coating, and because it only adds 1.46kg per square metre, it's infinitely more viable than using heavier, hardier materials.
Formerly part of the UK Atomic Energy Authority, Zircotec originally developed the coating to help manage the heat in nuclear reactor pipes. Then, in 1994, Prodrive approached them to see if the coating could be applied to reducing the cockpit temperatures of their Subaru rally cars.
After veering into motorsport, the coating was picked up by several supercar manufacturers and is standard fitment on the Ariel Atom V8, Lamborghini Murcielago SV, and Reventon.
Advertisement - Page continues belowBRICK KILN GROUP
If you're a bit weird, you'll know that the underside of the 1987 Benetton-Ford B187 front spoiler was painted black. You might even know that it was finished in a light-absorbing satin hue. But you probably won't know that the company responsible for that tiny, singular job back in the eighties has now grown to become Britain's leading F1 paintshop.
There's proper artistry to this - the difference between a well finished rear wing and a shabby one translates to about two thousandths of a second per lap. Or the difference between first and fourth place. Which probably explains why it takes up to six months on-the-job training on top of a normal apprenticeship before painters are let loose on team cars.
There's a weight issue, too - it's all well and good preparing a slippery wing, but it can't be a gramme heavier than a team's very strict kg-per-square-metre target.Working with carbon body panels and chassis poses its own unique problems, too. Firstly, it's a material with lots of holes in, so it's a bit like painting a very complicated waffle. Secondly, because it's so thin and relatively delicate, each paintjob is only good for one race (two for a chassis).
The latter doesn't sound too problematic, but you can't remove old paint with a chemical cleaner because it'll damage the carbon - it all has to be done by hand. Add to that the ludicrous time pressure of F1 (it's not unusual for Brick Kiln to turn around a chassis in 24 hours) and you realise just how well-oiled this team has to be to open its doors in the morning. And it explains how Brick Kiln manages to get through 4000 rolls of masking tape and 5000 paint filters every season.
Fancy getting you car painted by bonefide F1 sprayers? Unbelievably, BKG charges F1 teams the same labour rate as they do to the general public...PRIMARY DESIGNS
At the quiet end of an industrial estate in Oxfordshire, there's a shed that's home to 90 years worth of motorsport experience, including time served at Williams, Benetton and Renault F1. In it, men potter around quietly turning sheets of thin Inconel into full-blown Formula One exhausts.
Thumbing through the sheets of metal, Managing Director, Pat Barrett, explains: "An exhaust's got two main functions - removing gas and scavenging waste gasses so they induce cylinder filling. The first bit's pretty simple - pulses of exhaust gas leave the cylinders and flow through the primary pipes into a collector, which is the bit of the exhaust where the pipes merge.
"The second bit maximizes the high velocity travel of pressure waves down the primary pipe, - if you get the physics right, you can help the cylinders fill back up with air and fuel, maximizing the power and torque. And we build the whole thing from flat sheet metal for several teams right here."Based on CAD designs from team engineers, it takes Pat and his 14-strong staff over 100 hours to scratch build an F1 system - the collectors alone take 30 hours - and it takes four blokes, each with their own unique skill set, to hand finish every exhaust.
The nickel alloy used to build the systems is only 0.5mm thick, so there's not much margin for error. To add to the disaster potential, the team uses a unique and top-secret welding gas that's fiendishly tricky to master - both of which make the company's five-per-cent wastage figure all the more impressive...
Before an exhaust finds itself on the grid, the inside of the pipework's purged with argon, it gets satin polished to spot any imperfections and then it's examined under a microscope - because the metal's so thin, even the tiniest welding imperfection can cause cracks.Advertisement - Page continues belowBF1SYSTEMS
Diss, Norfolk. Home to the Bressingham Steam and Gardens experience, Frenze Beck Nature Reserve, much livestock and BF1Systems, suppliers and manufacturers of the electronic and composite components used by all but one F1 team on the grid.
Despite the, umm, incongruous surroundings, bf1systems develops and builds cutting edge sensor technology, monstrously complicated wiring looms, carbon components and the Aston-Martin One-77 (though the latter is a push-bike spin-off of the elusive hypercar...).
The company's latest innovation is proving pertinent this season too. It's developed a one-of-a-kind infrared monitoring system that measures the tyre's pressure, air temperature and even the carcasses' temperature. It's been a bit tricky to develop, though - while it only weighs 30 grammes on its own, it adds 90kg of weight to each wheel with the centrifugal force and experience temperatures of up to more than 150°c.But even though the components the company deals with are tiny, this is a very large shed. That's largely because bf1systems needs to house its 96 staff and it manufactures carbon fibre; the latter requires a massive great big autoclave that cures the composite by applying 220psi of pressure and 350°c of heat.
Lightweight pushrod ends for several teams have been made here, which not only meet savage aerodynamic design demands, but incorporate force sensors - the information these very clever little microprocessors provide data calibrated against temperature for everything from downforce settings to damper rates and ride height. The numbers it produces also find themselves on those £40k-a-pop F1 steering wheels, too.
bf1systems does lots of really quite wondrous stuff with wiring looms (that can take nearly 200 hours to build), too. As well as twisting each racing loom into perfect concentric circles so they don't lose shape, they manufacture one-off systems for concept cars. Remember the hugely awesome one-piece carbonfibre wiring loom for the Jaguar C-XF concept? Yep, that was this lot.Advertisement - Page continues below
Trending this week
- Car Review
BMW 3 Series Touring