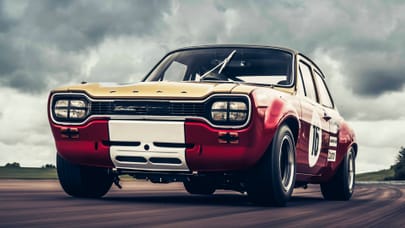
Exclusive: inside Andy Green’s 1000mph office
I’m hanging upside down by my ankles, much like a fruit bat, with an iPad in my hands. It displays a driver’s eye view from the cockpit of Bloodhound SSC, out through a narrow slot of windscreen as an endless desert rushes under the wheels. Blood floods to my head and the veins in my temples become purple and wormy. When I tilt the pad to the left – effectively it’s my steering wheel – the car veers to the right. Tilt it right and it goes to the left. Weird. Somebody shakes me and the screen goes fuzzy. Suddenly I’m flipped upright and something escapes from my nose and onto my shirt.
I’ve just broken the sound barrier. Virtually, at least. Because, while I might feel lightheaded and discombobulated, all of this is actually happening in a warehouse at the scrubby end of Bristol. Don’t worry, I’ve not been kidnapped. I’m doing this voluntarily, to gain a small insight into what Andy Green may experience when he attempts to drive Bloodhound for real – at 1,000mph – at the Hakskeen Pan in South Africa in 2016. Of course, he won’t be hanging upside down or expelling little green things through his nose, but with all the g force, he’ll feel like he is.
He will also feel as if a hurricane-force wind is being funnelled directly into his ear. Not only because Bloodhound pierces the air at supersonic speed, but also because that air must be slowed to a subsonic 550mph before entering the engine, to avoid blowing it up. This deceleration and subsequent shockwaves occur above his head on the roof of his canopy. And although he’ll be wearing a helmet and earplugs, the sound will still be terrifying. I’m played a simulation through a giant speaker stack, of the sort preferred by deaf rockers. It rumbles the ground and hits you right in the chest.
Here's the time we delivered the Bloodhound's 1000mph wheels to the factory
You’ll know the Bloodhound basics by now: jet engine (from a Eurofighter) plus large rocket (hotter than a volcano) plus F1 engine (used solely as a fuel pump) equals 135,000bhp and one thousand miles per hour. For the last seven years it has existed mostly in the minds of engineers and in renderings on computers. More recently it has started to take shape on a factory floor. As it edges closer to completion, new bits arrive at the back door of the warehouse every day, from 250 suppliers around the world. Only one per cent of parts are rejected, which means assembly has been swift, and last week they attached the carbon fibre monocoque – the cockpit – to the front end.
It’s Andy’s 1,000mph office. Being a generous chap, and a figurehead for the most interactive engineering project ever, he’s letting me sit inside it. Which makes TopGear.com the first media to do so. Don’t mind if we do. The canopy is off today, and eventually Andy will enter through a small hatch. For now though, from a platform beside the car, you straddle the blue bodywork and hang a leg into the cockpit. It’s quite deep. Hoik the other leg over and – with both feet on the seat – wiggle down in the same way you’d enter any other single-seater. But unlike an F1 car, there’s actually some elbow room, and in terms of space it’s more like an aircraft cockpit than a racing car’s. Andy is a Royal Air Force fighter pilot, after all.
I, on the other hand, am a short man from the West Country, so I imagine he’ll see over the dashboard better than me. It feels like I’m propped up on a sun lounger. But looking where he’s going is the easy bit. There’ll be a faint white line to follow down the 12-mile stretch of desert, which should help him to keep it straight. He’ll also have one eye on the instruments, the layout and configuration of which he designed himself. Just below eye-level are three, square display screens, below which is a sculpted steering wheel. On each side, around knee level, is a circular Rolex dial. At thigh height on each side are levers and control panels housing toggle switches and buttons.
That middle screen is the most important of the lot. It shows the car’s headline performance, including distance/speed/time info. There’s a digital interpretation of a traditional circular speedo, with a band around the edge to mark events on the way to its top speed. When to fire the rocket, for example. A bar graph rises to show how far he’s travelled. Two other bars rise and fall to show wheel loads and, so long as they’re on the ground, he’ll be happy. “I’ll have one eye dedicated to those…” says Andy.
The screen to the left shows system information – stuff such as hydraulic pressures, brake pressures and a skid detector. The screen on the right provides information about the three engines, including temperatures, pressures and fuel levels. And if all of these were to go blank, Andy will rely on the Rolex instruments – speedo on the left, chronograph on the right – to judge speed and time. They’re completely independent of the rest of the car, and carry their own GPS and battery. “These are the best instruments in the history of motorsport”, says Andy. If not the best, they’re certainly the most important…
Head this way for a 360 degree view of the Bloodhound SSC’s 1000mph cockpit
Top Gear
Newsletter
Thank you for subscribing to our newsletter. Look out for your regular round-up of news, reviews and offers in your inbox.
Get all the latest news, reviews and exclusives, direct to your inbox.
Then there’s the steering wheel, which is 3D-printed from titanium and matches the exact countours of Andy’s hands. It has three buttons on its left shoulder for the air brakes and parachute, and three on its right shoulder for radio comms and suchlike. Around the back are two triggers, one for Andy’s left index finger, another for his right. They’re nicked from a standard power drill, which Andy found in B&Q. One primes the F1 engine that’ll deliver 800 litres of hydrogen peroxide to the rocket in just 17 seconds. Five seconds later, Andy will pull the other printer to ignite the rocket. Boom.
Under his specially made Alpinestars boots – part of the most fireproof race suit in history – are two silvery metal pedals. They’re quite big and flappy, presumably to make them easier to find and less easily confused while g forces wreak havoc with leg muscles. Imagine strapping an Apple MacBook to each foot and you’ll be about right. The left pedal operates the wheel brakes below 200mph, at which point you can “pretty much get out and walk,” says Andy. The right pedal is a throttle for the jet engine. There’s no traction control.
The levers to his right shut off fuel to the jet engine. At these speeds, just throttling back gives extreme stopping power. Other levers allow him to deploy the air brakes and parachute manually, so if the computers go into meltdown, he can resort to good old muscle power. Either way, when the air brakes are up and the ’chute unfurled, he’ll experience deceleration of 60mph per second. That’s enough to generate 3g, which – as a fighter pilot – Andy is probably used to. “Imagine going from 60mph to a dead stop in one second. It’s that violent,” he says.
As I wipe my shirt with a tissue, I don’t doubt him for a minute.
Trending this week
- Car Review
BMW 3 Series Touring