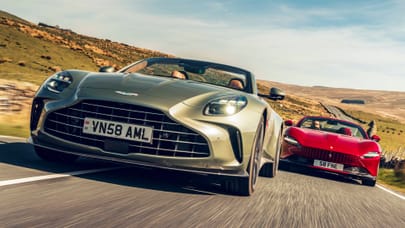
Just hit Ctrl+P: how to 3D-print a 700bhp supercar
Jack Rix meets the man behind the 3D-printed, Evo-engined DM Blade
“I’ve done wheelies in it. I’ve lifted the front wheels going up a hill in fourth gear by four or five inches,” says Kevin Czinger, founder and CEO of Divergent Microfactories. Fair to say, we like him already.
The wheelie machine in question is the DM Blade – the world’s first 3D-printed supercar that Czinger hopes to put into limited production, although that’s not actually the golden doughnut.
“The core company aim is to work with OEMs and licence the tech for higher-volume cars,” Czinger explains. “But within 18 months we’ll make a street-legal Blade, and sell a small run of the cars.”
Not every part of the blade is 3D-printed – the composite panels are made in a traditional way (although they could be printed in the future when the tech improves, say Czinger), as are perishables like brakes and tyres.
But it’s the aluminium and carbon-fibre chassis where the magic really happens.
Each car is constructed from 70 or so 3D-printed, aluminium alloy nodes. The largest takes around four hours to print, and the nodes are connected by carbon fibre rods.
“The chassis is like the motherboard, you just plug whatever components you like in,” Czinger says. “As a result it’s easy to adapt the system for anything from a two-seater to a pick-up truck.”
It's easy to adapt the system for anything from a two-seater to a pick-up truck
This is no off-the-shelf 3D printer. Czinger is working with one of the three-biggest 3D metal printing companies in the world and the process, called Direct Metal Laser Sintering (DMLS) where the piece is built up layer after layer, is improving all the time. Within 18 months Czinger expects the print time for a large node to reduce to between one and two hours.
In a nod towards lightness and affordability the engine isn’t an off-the-peg, locally-sourced V8, but a tuned version of the Mitsubishi Evo X’s 2.0-litre.
Top Gear
Newsletter
Thank you for subscribing to our newsletter. Look out for your regular round-up of news, reviews and offers in your inbox.
Get all the latest news, reviews and exclusives, direct to your inbox.
Specifically, it’s bored out to 2.4 litres, converted to run on CNG and fitted with a dustbin-lid Garrett turbocharger taking the output to a faintly absurd 700bhp and over 500lb ft of torque. The gearbox is a Holiger six-speed sequential chosen, say Czinger, for its “raw, racecar feel.”
Given the Blade weighs in at 630kg, that power figure starts to look like quite a lot, and explains why 0-60mph is apparently dispatched in 2.2 seconds. In fact, the Blade has nearly twice the power to weight ratio of a Veyron.
But before we get too carried away let’s put things in perspective – only the very first development prototype has actually been built, and there’s still another year of work at least to be done on the chassis before it has the structural rigidity of a Ferrari or Porsche.
Czinger’s grand vision is to reduce the materials, energy use, pollution and costs of car manufacturing – a process he calls ‘dematerialising’ – while allowing people to set up their own microfactories using his technique.
“Society has made great strides in its awareness and adoption of cleaner and greener cars. The problem is that while these cars do now exist, the actual manufacturing of them is anything but environmentally friendly,” Czinger says. If his 3D printing techonologies prolong the life of 700bhp combustion-engined supercars, we’re all for it...