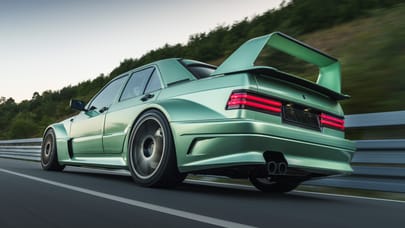
How to make a 1000mph wheel
Like a druidic medieval sacrifice, the blacksmith ceremonially lays the quarter-tonne lump of metal atop the flaming iron slab. Another smithy, squinting into the flames, cranks down his press, crushing the near-molten cylinder of pure aluminium into the shape of a beer barrel. Deftly, the first man grabs the barrel between a pair of giant forceps, spinning it through 90 degrees before the press comes crashing down again, flattening the metal once more. Over and over they go, the two men, peering through the steam and smoke, one flipping, the other pressing until, half an hour later, the metal is forged to a perfect disc, a metre across but just 15 centimetres tall.
It's all decidedly... Victorian. OK, so the blacksmith's press is a 3,600-tonne hydraulic monster, and his forceps are attached to the front of a decidedly nifty forklift-truck contraption, but still, this is manual labour - albeit awesomely skilled manual labour - with not a precision-guided laser nor microprocessor in sight.
This is how the world's fastest, most technologically advanced set of wheels is made: the wheels for Bloodhound, Richard Noble's land-speed-record car that, all being well, should do 1,000mph in the hands of Wing Commander Andy Green on South Africa's Hakskeen Pan; wheels that must withstand forces more extreme than any wheel has ever withstood before.
"This car is a cross between a fast fighter jet, an F1 car, a spaceship, a boat and a missile," explains Conor La Grue, former Royal Navy weapons engineer and now Bloodhound's lead commercial engineer. "And as a single component in Bloodhound, the wheel is the most complicated. This is the most advanced wheel in the world."
Hang on, asks TopGear naively. Isn't a wheel a wheel? Make it round, make it reasonably strong, job done? Afraid not, says Conor: any existing wheel would be instantly destroyed by the mind-boggling forces of a 1,000mph run. As it hits four figures, Bloodhound's rims will be spinning 10,200 times per minute: 170 revolutions every second, more than four times quicker than an F1 car's wheels will ever rotate. That means inconceivable centrifugal pull acting on the wheel's outer edges, exposing the rims to 50,000 times the force of gravity.
"If you took a piece of string the length of the radius of the wheel, tied a kilogramme bag of sugar to it and spun it 10,000 times a minute," explains Andy Green, "the bag of sugar would exert a load equivalent to 50 tonnes. More than a fully laden articulated lorry. It's a big number. And, of course, we're not looking at one bag of sugar, we're looking at 100 of them - because the finished wheel will weigh around 100kg. So the loads are phenomenal." A normal wheel would either deform like a doughnut from the hub, or shatter to pieces.
Bad news during a land-speed-record run. A broken wheel wouldn't only render Bloodhound lethally undrivable, but its fragments would instantly become ballistic missiles. "At 1,000mph, a quarter of a wheel has the equivalent energy of 300 tonnes," says Conor. "If a piece comes off, it's going straight through our monocoque, straight through the engine, straight out the back of the car. And straight through Andy on the way."
So Bloodhound's wheels have to be phenomenally, unprecedentedly strong. Which explains the rather industrial forging process we've just witnessed. Wouldn't it, TopGear asks, be better to pour the molten metal into, erm, a wheel-shaped mould? Conor shakes his head. That process - known as casting - is quicker, cheaper, more efficient and entirely fine for normal wheels: you know, the sort capable of a mere 300 or 400mph. But the microscopic cracks that form as a cast wheel cools would become fatal weaknesses when subjected to 1,000mph forces. In the forging process, however, the ‘grain' of the metal follows the shape of the wheel, meaning - at the molecular level - a far stronger, more uniform structure. Especially if it's been forged by Fuchs, the company most famous for making lovely wheels for old Porsche 911s.
As well as manufacturing tens of thousands of posh alloys each year, Fuchs also forges the finest aerospace components on the planet, including the nearest things to a Bloodhound wheel: compressor discs for jet engines.
The Bloodhound wheel makes jet fighters look simple. It starts with many tonnes of pure aluminium, which comes sloshing down the autobahn to Fuchs's Rhineland headquarters in molten form in the back of a tanker. Imagine if there was a crash. It'd be like a pastoral remake of The Terminator. Liquid metal safely received, Fuchs cranks it up to 700°C before adding alloying elements to create a brand-new super-strong metal, codenamed 70-37. A development of the alloy used in furthest aerospace, it's even hardier: the toughest aluminium ever created, in fact.
Top Gear
Newsletter
Thank you for subscribing to our newsletter. Look out for your regular round-up of news, reviews and offers in your inbox.
Get all the latest news, reviews and exclusives, direct to your inbox.
Once cool, this Popeye-spec alloy is cut into giant cylinders, four foot high by two foot across, which are popped into the oven until they're a toasty 400°C and as pliable as bread dough. Then they're subjected to the bashing, crushing, squeezing process TG has just witnessed. So hot and dense is the metal that the cheese, as the shaped disc is known, has to cool for an entire day before it can be handled. Over the next few days, Fuchs will forge some 18 cheeses for Bloodhound, enough for two full sets, a few spares and some wiggle room in case any emerge less than perfect.
Oh, but there's more. After forging, the cheeses are heat-treated and cold-compressed under 20,000 tonnes of weight. Then they're artificially aged, frozen, machined and inspected ultrasonically. "There are layers on layers of process. If Bloodhound were an onion, it'd be 400 miles across and have its own moon," nods Conor.
There's good reason for such diligence: at 1,000mph, even the smallest lumps of inanimate desert become bullets. Though volunteers have cleared some 6,000 tonnes of stone from the Hakskeen Pan, its surface is still covered in gravelly shards, impacting Bloodhound's wheels at supersonic pace. To find out what damage they might do during a record run, the Bloodhound team scooped up a few bags of Hakskeen Pan top layer, shipped them back to Britain... and then went about finding a gun capable of firing the ‘sabos' into the wheels at 1,000mph to see what damage they'd do to the alloy. "We looked right at the bottom of the impact areas, and there wasn't even the beginning of a crack," says Conor.
Which will, we suspect, come as a relief to Mr Green. But there's more testing to be done before these wheels can be bolted to Bloodhound. The team must spin a test wheel up to 10,000rpm, to check it doesn't distort, explode or plunge humanity into a parallel dimension. Which presents a couple of tiny issues: first, finding a facility capable of spinning a wheel fast enough, and, second, convincing its owner it's a good idea. "If we had a failure, we'd destroy the test facility," grins Conor. And the surrounding county, TopGear suspects.
But before that, the cheeses must be machined into, well, wheels. And for that they must head to the Castle Precision facility in Glasgow, where they'll be cut and finished to micrometre accuracy. So tight is the Bloodhound's schedule that the first cheese - forged the previous day, now compressed, machined and packaged up on a wooden pallet - has to be in Scotland by close of play this evening.
Click here to see if we can get it there... in a 510bhp Range Rover Sport.
Pictures: John Wycherley
This feature first appeared in Top Gear magazine